NEW BEST PRACTICES FOR ACHIEVING HIGH QUALITY AND HIGH THROUGHPUT
Petrographic thin sections have traditionally been prepared by hand. Skilled technicians work manually to produce consistent 30m thick thin sections for geological analysis. Preparation is difficult,time consuming and expensive, and requires extensive experience. As a result,laboratories have been established in low-cost countries. However, this has increased sample lead times, complicated interaction between geologists to laboratories and opened legitimate concerns about quality.
The key question facing geologists is how to combine high and repeated quality with high productivity,fast turn-around and low cost. The obvious answer is automation. Historically, thin section labs have had little automation and IT-enabled processes. Little has been done to automate thin section production and data capture processes. One reason for this is the lack of automated test equipment and modern information technology solutions.
The key to successful automation is to automate the entire end-do-end manufacturing process
Automating only one step simply shifts the bottleneck, and doesn’t deliver the required step-changein quality and efficiency.
Manufacturing process automation starts with a high quality, repeatable and consistent approach to gluing samples to glass plates. The sample must be perfectly aligned and pressed to the glass plate firmly with a constant force. The approach should be consistent and the same every time for best results. UV curable adhesives are used tospeed-up the process. Modern systems allow alternative use of heat or UV sensitive adhesives. For highest productivity several samples should be bonded simultaneously. Astera’s GLU10 represents the latest technology for achieving superior sample consistency, quality and throughput.
Following successful gluing, samples are cut down to a 100-200m thickness to save time in the next process steps of grinding and polishing. With cutting, it is critical to achieve an even and homogeneous result across the sample. Surface quality is only a secondary consideration. Also here, high throughput with multiple samples cut at the same time is the state-of-the-art. Astera’s CUT8 with Rock Straight™ technology, fulfills the most demanding process requirements.
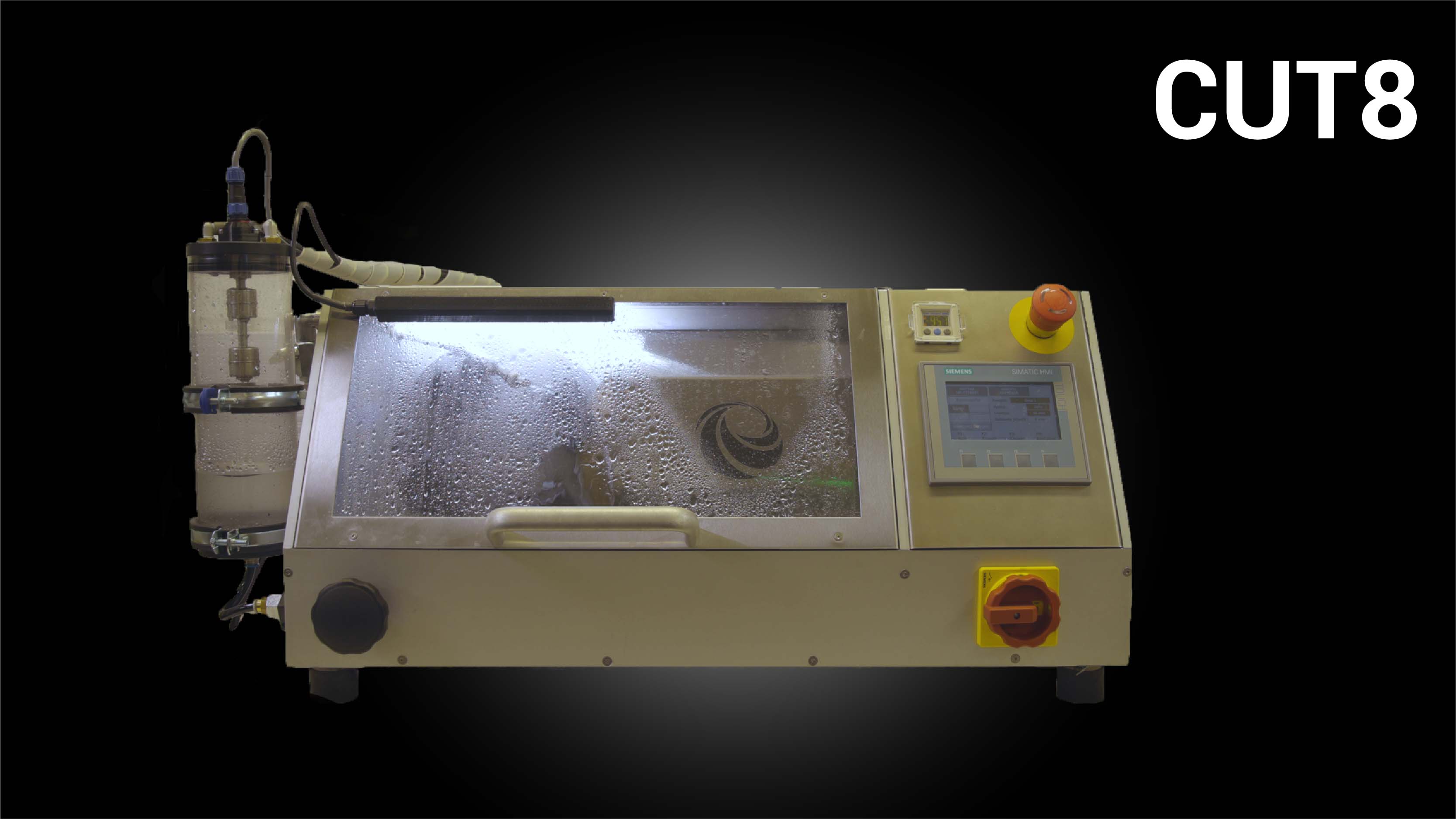
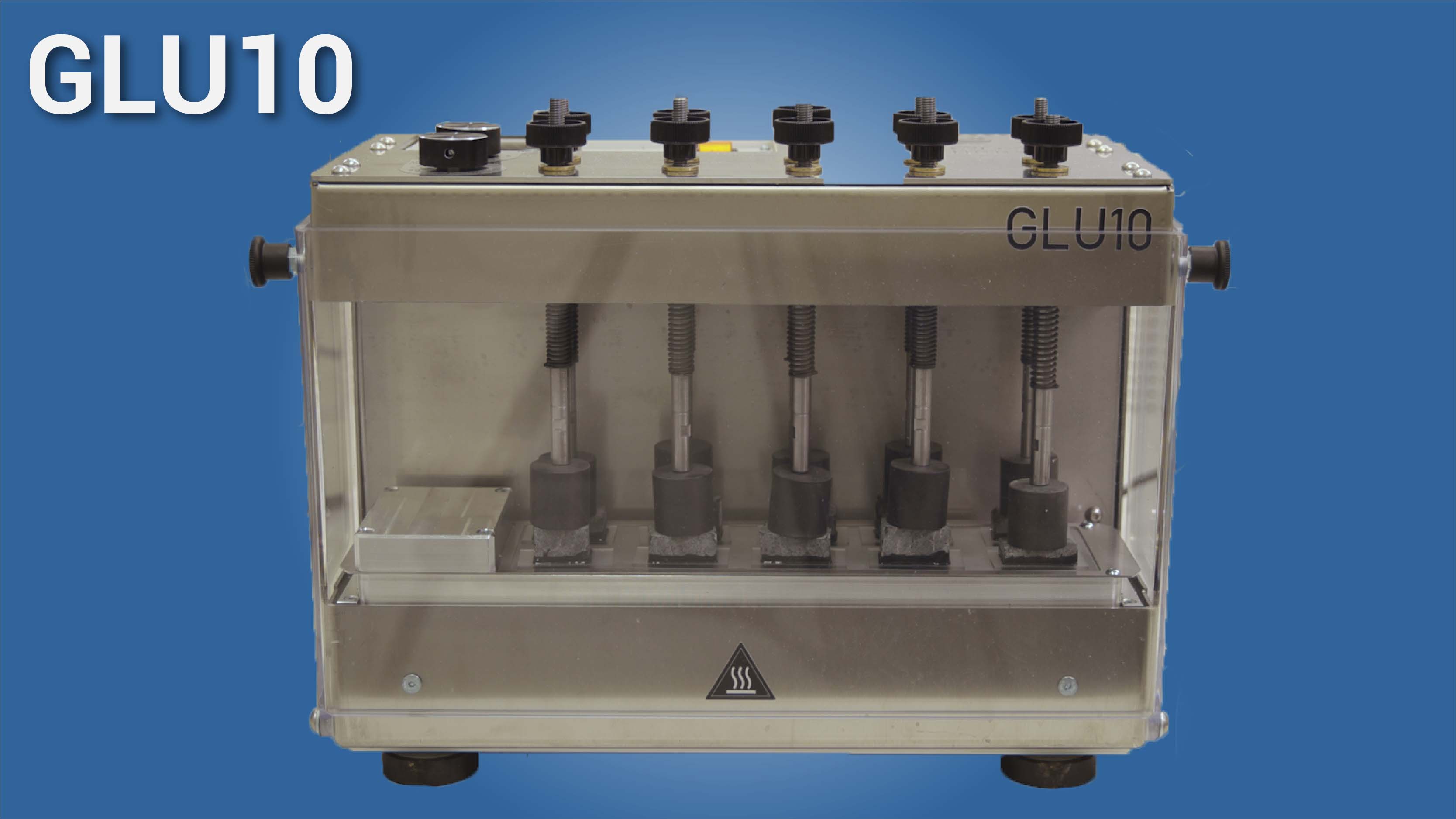
Save time and increase throughput with sequential process
The final steps in the process are grinding and polishing. Modern machines will perform the two processes sequentially, with only one sample set-up. The number of samples that can be processed with one set-up should be maximized to save time and increase throughput. As samples reach their final test thickness, adaptive machine controls kick-in to avoid any sample loss and optimize the quality. Astera’s GRN16 is a purpose-built machine for automated thin section grinding and polishing that achieves the highest quality, consistency and efficiency of any machines currently available. Full automation also reduces the requirement for trained personnel, while ensuring outstanding sample quality and consistency.
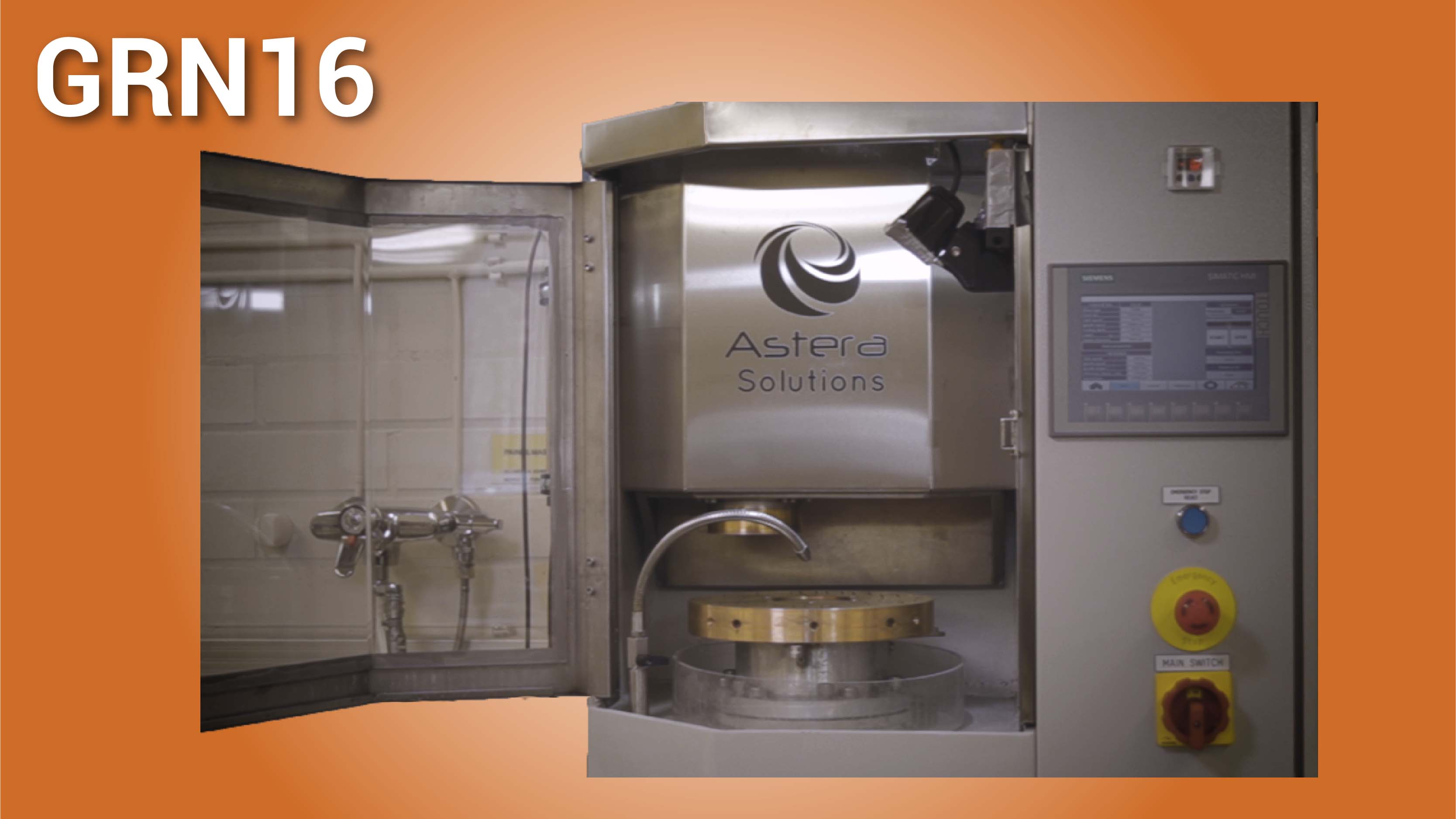
In summary, the key to achieving both high quality and consistency is to automate across the entire thin section preparation process. Investing in only one automation step simply moves the bottleneck to another part of the process. Astera’s GLU10, CUT8 and GRN16 comprise a unique suite of automated and integrated sample preparation machines that seamlessly covers all steps in the process. The most advanced petrographic test labs in the world are realizing the benefits of Astera’s technical solutions to increase process consistency while increasing efficiency.
Please contact us for more information on our high-performance sample preparation solutions.